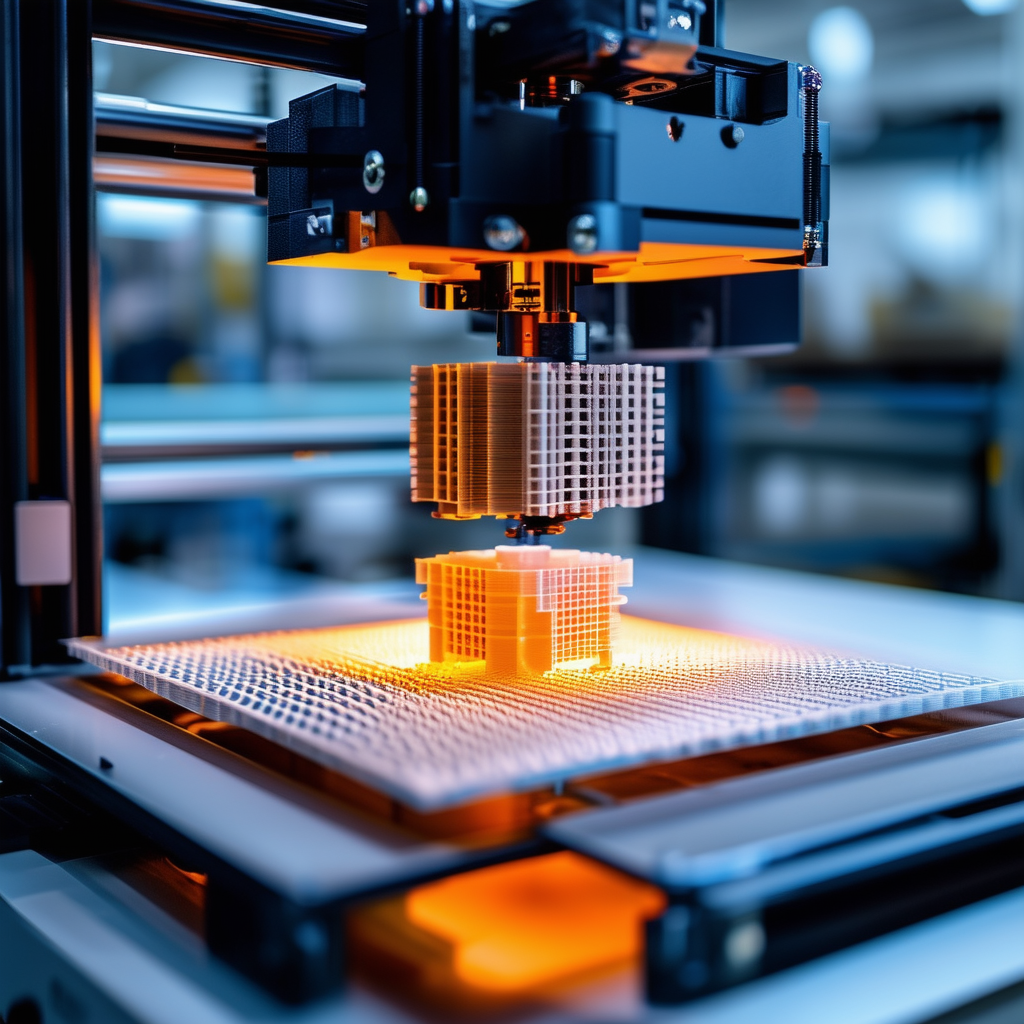
Discover how 3D printing is revolutionizing manufacturing by dramatically reducing production times and costs.
The Evolution of 3D Printing in Manufacturing
3D printing, also known as additive manufacturing, has come a long way since its inception. Initially used primarily for prototyping, the technology has evolved to be a crucial component in modern manufacturing processes. Early 3D printers were limited in materials and precision, but today's advanced systems offer a wide range of materials, higher resolution, and faster speeds.
Manufacturers across various industries, including automotive, aerospace, and industrial equipment, have begun to integrate 3D printing into their production lines. This shift is not just about keeping up with technology; it’s about reaping the numerous benefits that 3D printing offers, from reduced lead times to cost savings.
Key Benefits of 3D Printing for Accelerated Turnaround
One of the most significant advantages of 3D printing is the ability to produce complex geometries that would be impossible or highly time-consuming with traditional manufacturing methods. This capability shortens the design-to-production cycle, allowing for faster prototype testing and quicker iterations.
Additionally, 3D printing reduces the need for multiple manufacturing stages. Traditional methods often require separate steps for casting, machining, and assembly, but additive manufacturing can combine these steps into one, significantly speeding up the production process. This not only accelerates turnaround times but also reduces labor costs and material waste.
Real-world Examples of 3D Printing Successes
General Electric (GE) has successfully implemented 3D printing to manufacture fuel nozzles for their LEAP jet engines. By using additive manufacturing, GE was able to reduce the number of parts in the nozzle from 20 to just one, enhancing durability and cutting production time by 30%.
Another success story comes from Ford, which uses 3D printing to produce prototype parts for its vehicles. This approach allows Ford to test and validate new designs quickly, bringing innovative features to market faster than ever before. The company has reported that this method has cut prototype costs by up to 50%.
Overcoming Challenges in 3D Printing Implementation
Despite its benefits, implementing 3D printing in manufacturing is not without challenges. One of the primary hurdles is the initial investment in high-quality 3D printing equipment, which can be substantial. However, the long-term savings in production costs and time often justify this expenditure.
Another challenge is the need for specialized knowledge and skills. Operating and maintaining advanced 3D printers require a different skill set than traditional manufacturing equipment. Companies must invest in training their workforce or hiring skilled operators to fully leverage the technology. Additionally, quality control can be more complex with 3D printed parts, necessitating rigorous testing and validation processes.
Future Trends in 3D Printing and Manufacturing
As 3D printing technology continues to advance, we can expect to see even more significant impacts on manufacturing. One emerging trend is the use of multi-material 3D printing, which allows for the creation of parts with varying properties within a single print. This capability opens up new possibilities for complex and highly functional components.
Another trend is the integration of 3D printing with other advanced technologies such as artificial intelligence (AI) and the Internet of Things (IoT). AI can optimize print settings and predict maintenance needs, while IoT enables real-time monitoring of the printing process. These innovations will further enhance the efficiency and reliability of 3D printing in manufacturing.